Responsible for creating processing drawings. Promptly guide, handle and coordinate to solve technical issues that arise during production process.
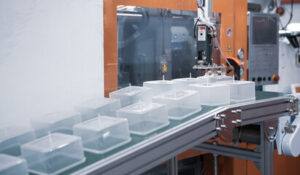
Family injection molds are ideal for low-volume orders as they reduce the need to run multiple cycles with different molds. This saves on time and materials and improves the cost-per-part. Read on American Plastic Molds for more information.
Injection moulding is a highly efficient method of producing plastic products for use in a wide range of industries. It allows for the production of large volumes at a relatively low cost, making it an ideal option for mass-production applications. Injection moulding produces parts that have good dimensional stability, meaning they will hold their shape and tolerances even when produced in high numbers. It also offers the flexibility of being able to include metal or plastic inserts. Injection moulding is capable of producing many different colours, and can be combined with other manufacturing processes to produce different types of polymers, including thermoplastics, thermosets, and resins.
The injection molding process involves using an injection machine to transfer molten plastic into a hollow cavity in the tooling mold. Once the plastic has been injected, it is allowed to cool and solidify before the gate of the cavity is sealed off. During this step, the pressure of the screw or plunger must be carefully controlled as excessive clamping can lead to part defects such as flashes and leakage. The injection speed must also be matched to the flow characteristics of the molten plastic to ensure a uniform wall thickness. Once the cavity is 95% full, the injection machine shifts to a holding pressure which compensates for thermal shrinkage and cooling.
After the product has fully solidified, the sprues and runners (the ‘tunnels’ through which the plastic material reaches the actual cavity) are cut off by the mould ejector system. The unused plastic is then reground and can be reused in the next cycle of production. Injection moulding has one of the lowest scrap rates of any manufacturing process, with a high percentage of the plastic used in production being recycled.
The tooling mold used for injection moulding is made from hard materials such as steel or aluminium to withstand the high temperatures and pressures involved in the process. It takes professional machinists to make this type of mold, which can take up to 20 weeks to create. Once it has been made however, the injection moulding process can be very fast.
Extrusion Moulding
Plastic extrusion is a high-volume manufacturing method that uses melted and formed polymer materials to create products with a consistent cross-section. It is particularly well suited to creating long tubular products, such as pipes and wire insulation. It is also popular for making products that require a smooth surface, such as straws and window frames. This process is typically more cost-effective than injection molding, especially when producing large quantities of similar parts.
The plastic extrusion process begins with plastic polymer pellets or granules being fed into the barrel of an extruder from a hopper. Once inside the barrel, the granules are gradually heated and pushed forward by rotating screws. The heat and friction create a continuous stream of molten plastic that passes through a die and cools to form the desired shape. Any excess material is gathered up and reused in future productions, reducing waste and machine downtime.
Because it uses less energy than other methods, extrusion moulding is a relatively green plastic manufacturing process. It is also able to produce a wide range of products in an extremely efficient manner. This makes it ideal for companies seeking to reduce their carbon footprint and environmental impact. It is important to note, however, that the production and disposal of plastic products has a significant impact on the environment, especially in terms of greenhouse gas emissions and climate change.
Injection molding has a higher initial design and tooling cost than other methods, but it is an excellent choice for projects that require detailed and intricate components. It is also ideal when a high number of identical products or components are required, as it reduces production and assembly costs by removing the need for post-production “clean-up” or rework.
The extrusion manufacturing process is ideal for producing a wide variety of different plastic products, including plastic pipes, straws, window frames and wire insulation. It is also suitable for producing thin plastic films and coatings, filaments and fibres, as well as products that replace glass or serve as alternative packaging. In contrast, injection molding is best suited for the manufacture of high-precision, three-dimensional shapes such as automotive parts, medical devices and toys.
Casting Moulding
Casting is a manufacturing technique that involves pouring liquid metal or plastic into a mold cavity to take the shape of a finished product. It can be used to produce large quantities of uniformly shaped parts with intricate designs that are difficult or impossible to make using other processes. It’s suitable for production of a wide range of products, from metal automotive components to small medical devices. It’s also relatively affordable, especially for large production runs because reusable molds can be used repeatedly.
This type of molding produces durable, high-quality products with superior mechanical properties. It is also suitable for producing components with complex shapes, tight tolerances, and a variety of surface finishes. It’s ideal for a range of materials, including polymers and some metals, as well as a variety of composites and ceramics. It’s also suitable for long production runs, and it’s easy to change the material composition of the product without having to invest in new tooling or a new process.
The casting molding process is quick and efficient, reducing production time and costs. This makes it a popular choice for the mass production of uniform, low-cost parts. It can also be used to create products with unique design features, such as undercuts or internal channels.
It’s also possible to use casting molding for a wide range of materials, including polymers and some metallic alloys. It can also be used for a wide range of sizes, from a few grams to a few tons.
Another benefit of casting is its high level of accuracy. It can be used to create parts with very precise dimensions, making it a good option for the manufacture of high-quality medical devices and consumer goods. It’s also possible to create parts with a hollow interior to reduce weight and materials usage. This is useful for decorative statuettes and figurines, as well as lamp bases and other items that require a hollow interior for aesthetic reasons. It’s also ideal for products that need to be lightweight, such as aeroplane propellers. It’s important to note, however, that casting is more prone to porosity and voids than other types of plastic molding.
Rotary Moulding
In this plastic molding method, powdered polymer is placed into a hollow mold which is then rotated slowly around two axes. It is heated while it is rotating so that the powder melts and ‘lays-up’ on the walls of the mould and forms the part. The mould is then cooled, often using air or water sprays. The finished part is usually very strong because it has no internal stresses and there are no sprues, runners or offcuts as with other types of plastic molding.
Another advantage of rotary molding is that it can create hollow one-piece construction products. This type of moulding is ideal for products that need to be lightweight, for example containers that hold liquids or gases such as flotation devices and rain barrels. Rotational moulding is also an excellent choice for making parts with a high degree of consistency. It can also be used to make parts with thick wall thicknesses. For this reason, if you are designing a new product, it is important to consider the draft angle in order to ensure that operators can remove the finished part from the mold easily and without damaging it.
The rotary moulding process is also very environmentally friendly as it uses no chemicals and produces no waste. This is a big advantage over other plastic molding processes, which can be extremely wasteful and which can also be harmful to the environment. However, it is worth noting that the pulverization of the plastic in the rotary molding process means that a lot of energy is needed and this can be costly.
Another disadvantage of this plastic molding process is that it can take a long time to make a part. This is because the rotary moulding machine needs to be heated up and cooled down multiple times in order to complete the cycle. This can be expensive, especially if the product is made of polyethylene. This is an area in which the research and development of new polymers needs to be continued in order to reduce production costs. Those that are developed should also be able to withstand the long heating cycles and should be easy to grind into a powder.